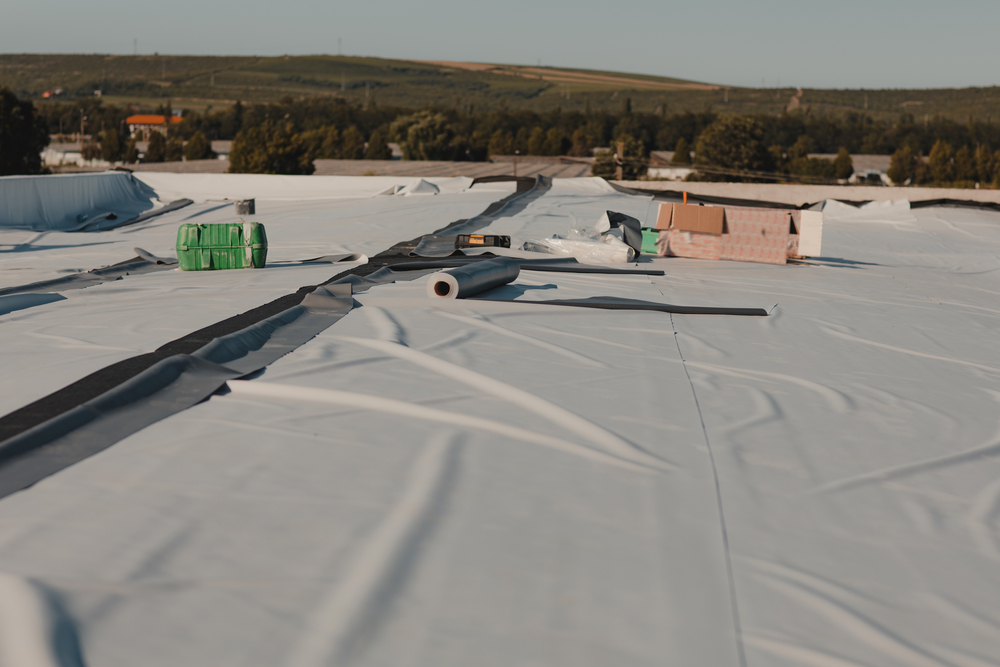
Can TPO Roofing be Repaired Easily?
December 20, 2024 7:39 pm Leave your thoughtsThermoplastic Polyolefin (TPO) roofing has become a go-to choice for many commercial buildings due to its durability, energy efficiency, and cost-effectiveness. However, like any roofing system, TPO roofs are not immune to damage and wear over time. This raises a common question among building owners and facility managers: Can TPO roofing be repaired easily? In this blog, we’ll explore the repairability of TPO roofing, its common issues, and how a commercial roof company can address them effectively.
What is TPO Roofing?
TPO roofing is a single-ply roofing membrane made from thermoplastic polyolefin. It is commonly used in commercial applications due to its reflective properties, which help reduce energy costs. The material is flexible, lightweight, and resistant to UV rays, making it an ideal choice for flat or low-slope roofs. However, like all roofing systems, TPO roofing is susceptible to wear and tear, especially in harsh climates or under poor maintenance practices.
Common Issues with TPO Roofing
To understand whether TPO roofing can be easily repaired, it’s essential to recognize the common issues it might face:
1. Punctures and Tears
TPO membranes can develop punctures or tears due to foot traffic, falling debris, or sharp objects. While the material is durable, heavy or repeated impacts can compromise its integrity.
2. Seam Failures
The seams of TPO roofing are heat-welded during installation. Over time, improper installation or constant exposure to extreme weather can lead to seam failures, which might result in water infiltration.
3. UV and Heat Damage
Although TPO is designed to resist UV rays, prolonged exposure to intense sunlight can cause the membrane to crack or degrade. Additionally, fluctuating temperatures can stress the material, leading to splits or shrinkage.
4. Pooling Water
Flat or low-slope roofs, including those with TPO membranes, are prone to water pooling. Standing water can weaken the membrane, increasing the likelihood of leaks and damage over time.
5. Improper Installation
In some cases, TPO roofing issues arise not from the material itself but from poor installation practices. Uneven application, weak seams, or insufficient bonding can result in early failures.
Is TPO Roofing Repairable?
The good news is that TPO roofing is indeed repairable, provided the damage is identified early and addressed promptly. The ease of repair largely depends on the extent of the damage and the expertise of the commercial roof company handling the job.
Factors Affecting Repairability:
- Extent of Damage: Minor punctures, tears, or seam issues can typically be fixed with relative ease. However, widespread damage or degradation might require more extensive repairs or even replacement.
- Age of the Roof: Older TPO roofs may be more brittle or deteriorated, making repairs more challenging. Newer installations are generally easier to repair.
- Expertise of the Repair Team: A skilled commercial roof company familiar with thermoplastic polyolefin roofing can diagnose and repair issues efficiently, ensuring long-lasting results.
Repair Techniques for TPO Roofing
Depending on the type and severity of damage, there are several methods to repair TPO roofing. Here are the most common approaches:
1. Patching
Patching is one of the most straightforward repair methods for TPO roofing. This involves cleaning the damaged area, cutting a piece of TPO membrane to size, and heat-welding it over the puncture or tear. Proper patching ensures a watertight seal and restores the integrity of the roof.
Steps Involved in Patching:
- Clean the damaged area thoroughly to remove dirt, grease, and debris.
- Cut a TPO patch slightly larger than the damaged section.
- Use a heat gun to weld the patch over the area, ensuring a secure bond.
2. Seam Repairs
For seam failures, repairing involves re-welding the affected sections. This process requires precision and the right equipment to ensure the seams are watertight and secure.
Key Considerations:
- The damaged seam must be cleaned and inspected.
- Heat-welding should be done at the correct temperature to avoid further damage.
- Post-repair testing ensures the seam is sealed properly.
3. Coatings
If the roof shows signs of UV damage or minor cracks, applying a reflective coating can extend its life. Coatings not only address superficial issues but also enhance the roof’s UV resistance and energy efficiency.
Benefits of Coatings:
- Prevent further degradation.
- Improve energy efficiency.
- Extend the overall lifespan of the roof.
4. Overlay System
For extensive damage that doesn’t warrant a complete replacement, an overlay system might be a viable solution. This involves installing a new TPO membrane over the existing one, creating a reinforced roofing system.
When to Consider Overlays:
- Significant damage but with a stable underlying structure.
- Budget constraints that make full replacement impractical.
Choosing the Right Commercial Roof Company
While TPO roofing can be repaired relatively easily, success heavily depends on choosing a reputable commercial roof company with experience in thermoplastic polyolefin roofing. Here are some tips to find the right partner:
1. Look for Experience with TPO Roofing
Not all commercial roof companies specialize in TPO roofing. Ensure the team you hire has specific experience and training in repairing thermoplastic polyolefin membranes.
2. Ask for References and Reviews
Check reviews and ask for references from past clients to gauge the company’s reliability and quality of work. A company with a solid track record will be more likely to deliver satisfactory results.
3. Verify Licenses and Insurance
Ensure the company is licensed and insured to protect yourself from liability in case of accidents or unforeseen issues during the repair process.
4. Request a Detailed Estimate
A reputable commercial roof company will provide a detailed estimate outlining the scope of work, costs, and timelines. Avoid companies that hesitate to provide transparent pricing.
Preventative Maintenance for TPO Roofing
To minimize the need for repairs and extend the life of your TPO roof, regular maintenance is crucial. Here are some tips:
1. Regular Inspections
Schedule bi-annual inspections with a commercial roof company to identify potential issues early. Inspections are especially important after severe weather events.
2. Clean the Roof Surface
Dirt, debris, and algae can accumulate on TPO roofs, leading to damage over time. Regular cleaning helps maintain the roof’s integrity and appearance.
3. Address Pooling Water
Ensure proper drainage systems are in place to prevent water pooling, which can weaken the TPO membrane.
4. Limit Foot Traffic
Excessive foot traffic can cause punctures or wear. Use walkways or mats to protect the membrane in areas where foot traffic is unavoidable.
Final Thoughts
TPO roofing is a durable and cost-effective choice for commercial buildings, and it is indeed repairable in most cases. The key to ensuring successful repairs lies in addressing issues promptly, using the right techniques, and partnering with an experienced commercial roof company. Additionally, regular maintenance can prevent many common problems, extending the life of your thermoplastic polyolefin roofing and maximizing your investment.
If your TPO roof is showing signs of wear or damage, don’t delay. Reach out to a trusted commercial roof company to assess the situation and provide expert solutions tailored to your needs.
Need a Roofing Company in Springfield, MA?
Since 1987, R & H Roofing has remained one of the most trusted names in the roofing industry. We specialize in commercial and industrial roofing and offer a wide variety of roofing systems including EPDM systems, TPO Systems, Metal Roofing Systems, BUR Tar & Gravel Systems, Asphalt Shingles, and PVC Systems. We also work with some of the leading manufacturers including Firestone, Carlisle, Duro-last, and Garland. Contact us today to learn more about what we can do for you!
Categorised in: TPO Roofing
This post was written by admin