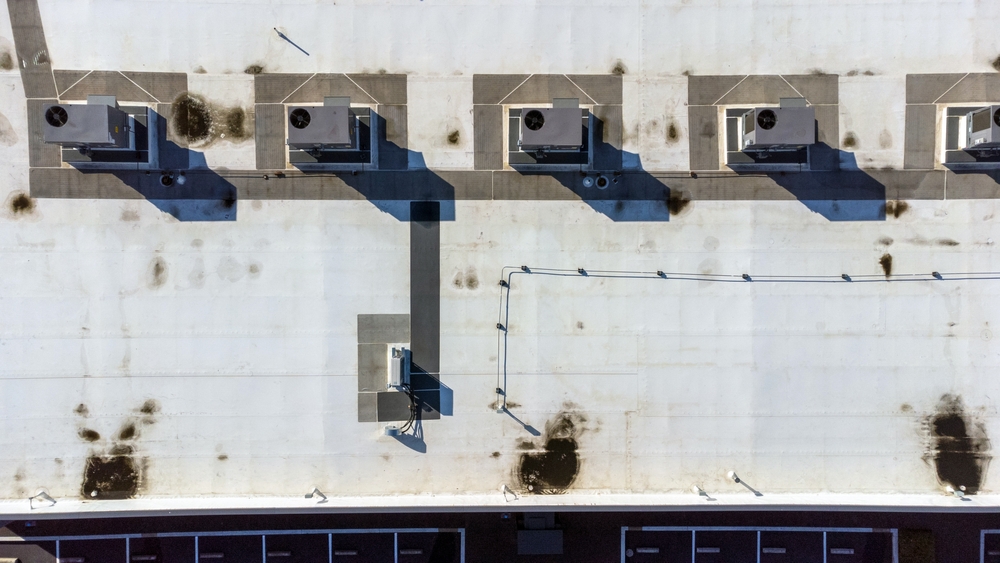
How can I Prevent Leaks in my Industrial Roof?
May 31, 2024 5:36 pm Leave your thoughtsIndustrial roofs are subjected to harsh weather conditions, temperature fluctuations, and structural stresses, making them prone to leaks and water damage. Preventing leaks in your industrial roof is essential to protect your property, equipment, and employees from potential water damage and costly repairs. By implementing proactive maintenance strategies and following best practices, you can minimize the risk of leaks and ensure the longevity and integrity of your industrial roof. Here are some effective tips for industrial roof leak prevention.
Regular Inspections and Maintenance
Regular inspections are crucial for identifying and addressing potential issues before they escalate into costly leaks. Schedule routine inspections of your industrial roof at least twice a year, ideally in the spring and fall, to assess its condition and identify any signs of damage or wear. Look for signs of cracked or missing shingles, deteriorated flashing, ponding water, and debris buildup on the roof surface. Addressing these issues promptly can prevent water infiltration and extend the lifespan of your industrial roof.
Proper Drainage Systems
Effective drainage is essential for preventing water buildup and leaks on your industrial roof. Ensure that your roof is equipped with adequate drainage systems, including gutters, downspouts, and roof drains, to channel water away from the roof surface efficiently. Clear debris and obstructions from gutters and downspouts regularly to prevent clogs and ensure proper water flow. Consider installing gutter guards or screens to minimize debris buildup and reduce the need for maintenance.
Sealant Application
Sealing vulnerable areas of your industrial roof can help prevent water penetration and leaks. Apply a high-quality sealant to seams, joints, flashing, and other penetrations to create a watertight barrier and protect against moisture intrusion. Choose a sealant that is compatible with your roofing material and can withstand exposure to UV rays, temperature fluctuations, and harsh weather conditions. Regularly inspect sealed areas for signs of deterioration or damage and reapply sealant as needed to maintain their effectiveness.
Roof Coatings
Applying a protective roof coating can enhance the durability and waterproofing capabilities of your industrial roof. Roof coatings create a seamless membrane that seals and protects the roof surface from water infiltration, UV damage, and other environmental factors. Choose a roof coating that is specifically designed for your roofing material and climate conditions. Consider factors such as reflectivity, thermal resistance, and durability when selecting a roof coating product. Apply the coating according to manufacturer guidelines and schedule periodic inspections and recoating as needed to ensure long-lasting protection.
Professional Roof Maintenance
Hiring a professional roofing contractor for regular maintenance and repairs can help prevent leaks and extend the lifespan of your industrial roof. Professional roofers have the expertise, experience, and specialized equipment to perform thorough inspections, identify potential issues, and address them effectively. Schedule annual or biannual maintenance visits with a reputable roofing contractor to keep your industrial roof in optimal condition and minimize the risk of leaks and water damage.
Emergency Leak Response Plan
Despite your best efforts at prevention, leaks may still occur on your industrial roof due to unforeseen circumstances such as severe weather or structural damage. Implementing an emergency leak response plan can help minimize the impact of leaks and prevent further damage to your property and assets. Develop a comprehensive plan that outlines procedures for detecting and reporting leaks, evacuating affected areas, containing water damage, and contacting emergency repair services. Train your staff on the emergency response plan and ensure that they are familiar with their roles and responsibilities in the event of a roof leak.
Roof Replacement or Upgrades
If your industrial roof is old, deteriorated, or prone to frequent leaks, consider investing in roof replacement or upgrades to improve its performance and longevity. Modern roofing materials and technologies offer superior durability, weather resistance, and waterproofing capabilities compared to traditional roofing systems. Consult with a qualified roofing contractor to assess the condition of your industrial roof and explore options for replacement or upgrades that best suit your needs and budget. Investing in a new roof can provide long-term protection and peace of mind, reducing the risk of leaks and water damage in the future.
Summary
Preventing leaks in your industrial roof requires proactive maintenance, proper drainage, sealant application, roof coatings, professional maintenance, emergency response planning, and, in some cases, roof replacement or upgrades. By implementing these effective strategies and following best practices, you can minimize the risk of leaks and ensure the integrity and longevity of your industrial roof. Protecting your property, equipment, and employees from water damage is essential for maintaining a safe and productive work environment. With regular inspections, maintenance, and proactive measures, you can enjoy a leak-free industrial roof for years to come.
Need a Roofing Company in Springfield, MA?
Since 1987, R & H Roofing has remained one of the most trusted names in the roofing industry. We specialize in commercial and industrial roofing and offer a wide variety of roofing systems including EPDM systems, TPO Systems, Metal Roofing Systems, BUR Tar & Gravel Systems, Asphalt Shingles, and PVC Systems. We also work with some of the leading manufacturers including Firestone, Carlisle, Duro-last, and Garland. Contact us today to learn more about what we can do for you!
Categorised in: Industrial Roofing
This post was written by admin